The procedure of CNC machining involves the usage of a computer system to regulate device tools for an extra trusted and consistent outcome. This modern technology translates CAD (computer-aided style) designs directly into machine-readable code, which overviews the machining process. The outcome is that manufacturers can create components with constant top quality and accuracy, minimizing waste and the threat of error in production. In the situation of copper, which can be fairly challenging to device as a result of its thermal conductivity, high ductility, and tendency to work-harden, CNC technology supplies the convenience needed to attend to these concerns properly. Specialized strategies and tools are typically used to optimize the machining process, which can consist of making use of reducing tools coated with difficult products to decrease wear and improve performance when dealing with soft steels like copper.
Discover copper cnc machining exactly how copper CNC machining merges innovative modern technology with lasting methods to generate complex, high-precision parts, driving technology throughout sectors such as electronic devices, auto, and aerospace.
Amongst the main advantages of CNC machining copper is the capacity to create complex forms that typical machining techniques may not accommodate. The repeatability of the CNC machining procedure makes sure that mass production of copper components preserves uniformity, thus fulfilling rigid industry criteria.
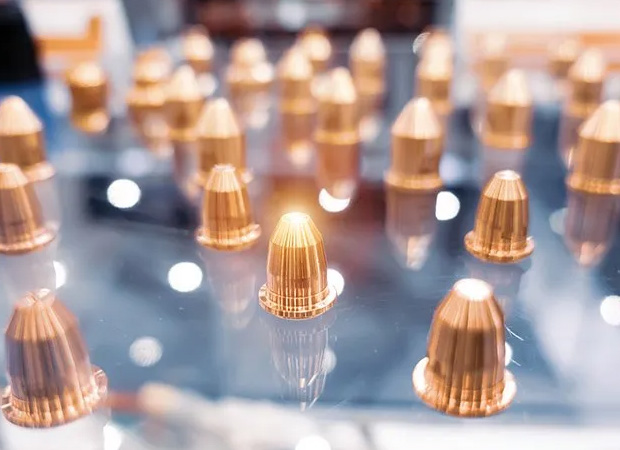
Temperature level management plays an important duty in the CNC machining of copper due to its capability to conduct warm swiftly. High-speed machining can lead to significant warmth generation, which may negatively influence the homes of the copper and aggravate tool wear.
The sustainability facet of CNC machining copper is not to be neglected. CNC machining, combined with lasting techniques, can decrease waste by enabling makers to make use of scrap copper from other processes.
In enhancement to sustainability, cost-effectiveness is an additional critical element for makers picking CNC machining for copper parts. The first financial investment in CNC machinery may be considerable, the long-lasting advantages can surpass the prices. CNC machining provides a reduction in labor expenses as a result of its computerized nature and lessens the need for comprehensive hands-on treatment. The exact control & repeatability supplied by CNC technology reduces scrap rates, reducing material expenses. In addition, for tiny to tool batch production runs, CNC machining can prove much more economical compared to standard machining processes, as it enables smooth modifications and style modifications without considerable retooling. This capability to pivot swiftly can be useful, specifically in busy sectors where market needs can shift unexpectedly.
Furthermore, as innovation develops, the performances within CNC systems are expanding, further enhancing the capacities of copper machining. The combination of simulation software permits suppliers to anticipate potential issues prior to the machining process begins. These simulations allow better preparation of device courses and elucidate just how the copper material will react throughout the machining procedure. By recognizing and attending to prospective difficulties ahead of time, companies can reduce downtime and increase productivity, creating a smoother operational flow.
Competent machinists must be experienced in interpreting layout specs, selecting the proper tools, and readjusting machining parameters to minimize problems associated with copper's special machining attributes. Hybrid machining, which incorporates standard CNC machining methods with additive production, is emerging as a feasible method for creating detailed copper components, mixing the toughness of both innovations and possibly transforming how makers approach copper production.
In the world of research and growth, CNC machining is aiding the exploration of brand-new copper alloys to enhance efficiency better. By synthesizing copper with products such as aluminum, nickel, or tin, makers can engineer composites that have actually improved stamina, electric efficiency, and resistance to wear and rust. These technologies could cause arising applications in sectors that rely heavily on conductive products, such as renewable energy and electrical vehicles. Furthermore, as international industries work towards better energy efficiency, copper's function as a conductor in digital circuits will certainly remain vital, driving demand for sophisticated machining options.
The aerospace and automobile markets are likewise keen adopters of copper CNC machining, particularly where lightweight components are of critical importance. As the shift towards hybrid and electrical lorries proceeds, the need for high-performance copper elements will likely surge, thus pushing the requirement for sophisticated CNC machining methods that guarantee efficiency and quality in production.
As CNC machining technology remains to create, it permits more automation, where basic procedures such as tool changes, inspections, and maintenance can be set right into the manufacturing cycle. This development implies that producers will be able to attain greater efficiency levels, shorter lead times, and greater adaptability in suiting personalized demands or variations in design. As a result, organizations that involve in CNC machining operations are better matched to pivot in feedback to the changes in consumer and market demands, cultivating development in a progressively competitive landscape.
Discover countersink size chart how copper CNC machining combines innovative innovation with sustainable practices to generate complex, high-precision components, driving technology throughout markets like electronic devices, vehicle, and aerospace.
The worldwide marketplace for CNC machining of copper is observing considerable growth, affected by aspects such as the increase of smart modern technologies, electric vehicles, and recurring initiatives to enhance energy effectiveness across various applications. It mirrors a merging pattern where businesses embrace electronic production practices, helping form the future of manufacturing. Establishing collaborations with providers, technology providers, and academic community can improve access to the current advancements and understanding within the field, cultivating a collective environment that drives forward-thinking campaigns. In this training, evolution and ability development continue to be critical; purchasing workforce education and learning on CNC machining methods, innovations, and product sciences will certainly equip manufacturers to remain ahead of the contour.
In conclusion, the combination of CNC machining with copper materials uses a distinctive competitive side for producers in today's busy industrial landscape. Its capability to supply high precision, minimize manufacturing time, and allow intricate designs makes CNC machining a crucial component of contemporary production practices. Coupled with sustainability initiatives, cost-effectiveness, and possibilities for development, the CNC machining of copper not only fulfills the demands of contemporary applications yet also lays the groundwork for the future trajectory of production in numerous industries. As markets advance and the boundaries of innovation increase, embracing CNC machining's potential will certainly be vital to realizing unmatched development and technology in the utilization of copper products. The harmony of copper's product properties with sophisticated CNC machining strategies proclaims a new age in which sustainability, precision, and effectiveness job together to develop revolutionary components that will define the future of production and past.